Essay/Term paper: The mobot project: longwood
Essay, term paper, research paper: Science Reports
Free essays available online are good but they will not follow the guidelines of your particular writing assignment. If you need a custom term paper on Science Reports: The MOBOT Project: Longwood, you can hire a professional writer here to write you a high quality authentic essay. While free essays can be traced by Turnitin (plagiarism detection program), our custom written essays will pass any plagiarism test. Our writing service will save you time and grade.
The MOBOT Project: Longwood
In modern engineering, a systematic approach is used in the design,
operation, and construction of an object to reach a desired goal. The first step
of the process employs what is commonly known as the scientific method. The
next step involves forming an interdisciplinary team of specialists from not
only the various engineering disciplines, but from other fields whose knowledge
may be useful or even necessary to completing the project. This step doesn't
apply to our project, due the confined nature of the class. Finally,
considerations must be taken into account to ensure that the project is
efficient as well as cost effective.
The goal of the MOBOT Project was to design and build a programmable
robot. The robot had to complete a series of four movements in four given
directions over a distance of at least 6 inches. Power and weight restrictions
were applied to ensure the safety of the students and, more importantly, the
teacher. As the goals of the project were made clearer, our group began
discussing possible ideas for the design. There were some disagreements about
whether we should take the electromechanical route or the purely electrical one.
And after some deep thought, we all agreed that the mechanical way would be the
simplest to build and the most merciful on our pocketbooks. Even though we were
coming up with some good ideas, each design seemed to contain some major
problems. One of the reoccurring problems dealt with the synchronization of the
driver motor and the steering system. Finally the team came up with a design
that allowed the drive and steering controls to be independent of one another,
but still allowing each one to be linked in time. This design has now become
what is known as LONGWOOD.
The Longwood is divided into two main parts: 1)motion system and 2)logic
board. As the engineer, I was responsible for motion design. Therefore, that
will be the focus for the remainder of this section.
The main components of the motion system consist of a platform, three
wheels, a wheel frame, two motors, and two contact switches. Two of the wheels
were connected to a motor and attached at the front end of the platform. These
wheels were only allowed to move simultaneously in either a forward or reverse
direction. The third wheel was hooked up to the wheel frame and free to rotate
approximately 45 degrees in either direction. Figure 1.1 shows an illustration
of how the wheel frame works. The wheel frame and third wheel were then
attached to the platform completing the basic assembly. The second motor was
put near the end of the platform and is used solely to pull the logic board
through a series of contact points. The final step involved setting up a canopy
containing the contact switches across the platform where the switches were free
to strike the logic board.
The fact that the wheel base can be controlled separately from the
forward and reverse motor yielded some advantages that we thought were rather
interesting. One of them is that the robot is able to make a turn while driving
in reverse, instead of just forward. Another feature is that the car is capable
of turning and then translating in one command. Even though this was one of the
original parameters which was eliminated because it complicated matters, we felt
that it couldn't hurt to have it anyway. The theory of the motion design was
finished. The only obstacles that remained were the testing and fine-tuning of
Longwood, a machine that was destined for success.
Other sample model essays:
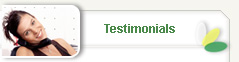

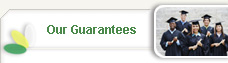

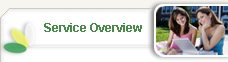

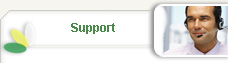

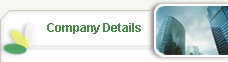
